Since the days of Kitty Hawk, propeller-driven engines have been at aviation’s forefront — even today’s jet-powered turboprops are arguably mere extensions of this century-old technology. Now NASA and companies such as General Electric and Rolls-Royce are developing a new generation of fuel-efficient “open rotor” engines that are definitely not your granddaddy’s propeller.
The goal is to introduce these new engines into a regional jet market with the promise of boosting airlines’ struggling bottom lines while meeting future international fuel-efficiency standards.
Open-rotor engines are still powered by a jet turbine, as are current turbofan engines. But their blades are not covered by a conventional turbofan’s nacelle — its readily identifiable, tube-like jet housing. Instead, these new engines’ rotors are exposed to the open air, like traditional propeller-driven engines. Unlike their conventional prop cousins, an open rotor’s blades are mounted at the rear, not the front, of the engine.
Both the U.S. Federal Aviation Administration and CFM International, a joint venture between GE Aviation and France’s Snecma, are involved in this effort to design and test an extremely fuel-efficient open-rotor engine. When mounted on next-generation airframes, this new technology may cut fuel consumption by as much as half when compared to conventional turbofan engines.
“Advances in computer analytics and high-tech testing enable us to optimize the fan blades to meet the sometimes conflicting design requirements of efficiency, acoustics, and durability,” said Randy Vondrell, advanced products manager at GE Aviation.
Aerodynamic and acoustic tests started on scale versions of the open rotors in late 2009 at NASA’s Glenn Research Center.
An early version of the open-rotor engine, the GE-36 propfan, was tested on Boeing 727 and MD-80 aircraft in the 1980s.
But by the time the technology had reached maturity, the oil supply disruptions of the 1970s were forgotten and fuel prices had tumbled. The technology languished as a result. Over the past five years, however, the U.S. and Europe have been researching a new generation of the propfan, now dubbed open rotor.
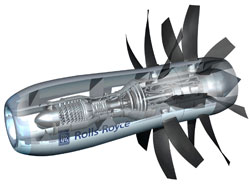
An artist’s rendering of a Rolls-Royce open-rotor engine. (Rolls-Royce)
“Today, almost 60 percent of an airline’s direct operating costs come from fuel consumption,” said Juan Alonso, a professor of aerospace engineering at Stanford University. “When you only have a profit margin of 1 or 2 percent, this open-rotor fuel reduction could offer significant savings.”
The savings over a plane’s 20- to 30-year lifespan, says Alonso, would amortize the cost of either retrofitting an existing fleet with open rotors or buying whole new aircraft with these advanced engines already installed.
The key to these fuel savings comes from the open-rotor engine’s higher “propulsive efficiencies,” simply meaning how efficiently an engine’s mechanical energy is turned into thrust.
A little aeronautical engineering helps explain this. Turbojets, like those used on the first jet fighters, offer the least propulsive efficiency since their air intake is routed through the engine’s core, where the air is compressed and then combusted with fuel to give the turbojet its thrust.
But traditional turbofans divert a portion of the energy from the jet turbine into driving a fan, which in turn compresses a secondary source of air, reducing noise, and producing more thrust. Turbofans also have larger fans, which helps raise their propulsive efficiency.

The one-fifth-scale forward and aft blades of the GE open-rotor engine.
“We’ve been trying to grow these turbofan diameters larger over time because they’re more efficient propulsors that way,” explained Dale Van Zante, an aerospace engineer at NASA Glenn Research Center. But larger fans mean larger housings, which means more weight (and lower mileage). “So the next step is to get rid of the nacelle.”
Van Zante says that current designs call for an open-rotor diameter of about 14 feet, roughly double the diameter of a rotor on a CFM 56 turbofan engine, which typically powers the single-aisle Boeing 737.
Two rows of scimitar-shaped blades would be mounted at the rear of the engine, 12 blades in front and 10 in back. The front blades rotate clockwise, while the back blades rotate counterclockwise. That opposite rotation enables the engines to maximize their thrust.
Engineering concerns suggest that the first open rotors would be installed on aircraft flying shorter routes, says Van Zante. As Alonso explains, “For transoceanic travel, you would need some very large open rotors,” which would present an installation problem, especially for wide-body aircraft.
These regional jets, however, would be faster. Today, conventional turboprops are limited to flight speeds of around Mach 0.55 (Mach 1 is the speed of sound at sea level). But Van Zante says these open-rotor engines would hit speeds approaching Mach 0.8, almost matching aircraft powered by the fastest turbofans.
Although open-rotor engines are noisier than today’s turbofans, the consensus is that they will be able to meet current FAA noise requirements. GE Aviation is working with the FAA on other potential issues with open rotors, such as blade icing, bird strikes, even how an aircraft would cope with a flung rotor blade.
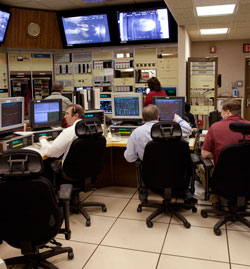
The control room of the high-speed wind tunnel at NASA’s Glenn Research Center during the testing of the one-fifth-scale forward and aft blades of the GE open-rotor engine.
Since the rotors are expected to be mounted toward the back of the aircraft, additional protective material would be built into the fuselage to ensure it would not be catastrophically breached in the event of a flung blade, which besides imperiling passengers could potentially sever cables and hydraulic lines.
In principle, the aircraft would be designed to fly safely on only one engine. Thus far, there haven’t been any deal breakers, and interest in the technology appears to be growing.
British engine manufacturer Rolls-Royce is also involved in an effort to develop open-rotor engines as part of Europe’s SAGE (Sustainable and Green Engines) program. A one-16th-scale engine design has already undergone test runs and Robert Nuttall, Rolls-Royce’s vice president of strategic marketing for civil aerospace, says the company is working with airframe manufacturers like Airbus and Boeing to address what it calls the open rotor’s “installation challenges.”
Nuttall says his company’s own open-rotor design would offer an immediate 30 percent fuel-burn reduction over current conventional turbofans, with a 30 percent reduction of CO2 emissions and a 60 percent reduction in nitrogen oxides.
Assuming a third of the world’s single aisle commercial aircraft engines are replaced with open rotors, Alonso would envision a global CO2 emissions reduction of at least 10 percent.
The European initiative expects to test a full-scale open-rotor engine in 2016. However, a commercial installation of an open rotor isn’t projected until the middle of the next decade.
Beyond that, Vondrell says, “the ultimate future of the open rotor is still wide open.”
Sign up for the free Miller-McCune.com e-newsletter.
“Like” Miller-McCune on Facebook.
Follow Miller-McCune on Twitter.
Add Miller-McCune.com news to your site.
